
Published: Last Updated:
Readtime: 9 min
Every product is carefully selected by our editors and experts. If you buy from a link, we may earn a commission. Learn more. For more information on how we test products, click here.
You don’t understand a car manufacturer until you visit their factory, and that’s especially true for Lamborghini. History, television, and other brands would have you believe that this is some small-time tractor manufacturer in Sant’Agata Bolognese who managed to squeeze a V12 engine into some scaffolding and add wheels to it. However, in reality, this is one of the most impressive factories we’ve ever visited.
They might have a dedicated carbon fibre facility and state-of-the-art automation, but what impressed us the most about our visit to Lamborghini’s factory was how they’re balancing the traditional with the cutting-edge. Nonna is still over there sitting at the sowing machine hand-stitching your leather seats together, and she has been for more than 30 years, while in the other corner of the factory, a master engine builder who treats his job like some kind of life-or-death situation is adding the cylinder heads to the 6.5-litre V12 in your new AUD$987,000 Lamborghini Revuelto.
Their flagship model might be expensive (and unobtainable) for most, but when you see what goes into making the new Revuelto, and the recently unveiled Temerario, which is yet to be priced in Australia, it’s truly impressive and you begin to justify the cost. Still, you can make your mind up for yourself once you’ve seen everything that we experienced in the Lamborghini Factory. Let’s take a look!
RELATED: ‘The Last Dance’: Lamborghini Huracán STJ is Faster and Uber Limited.
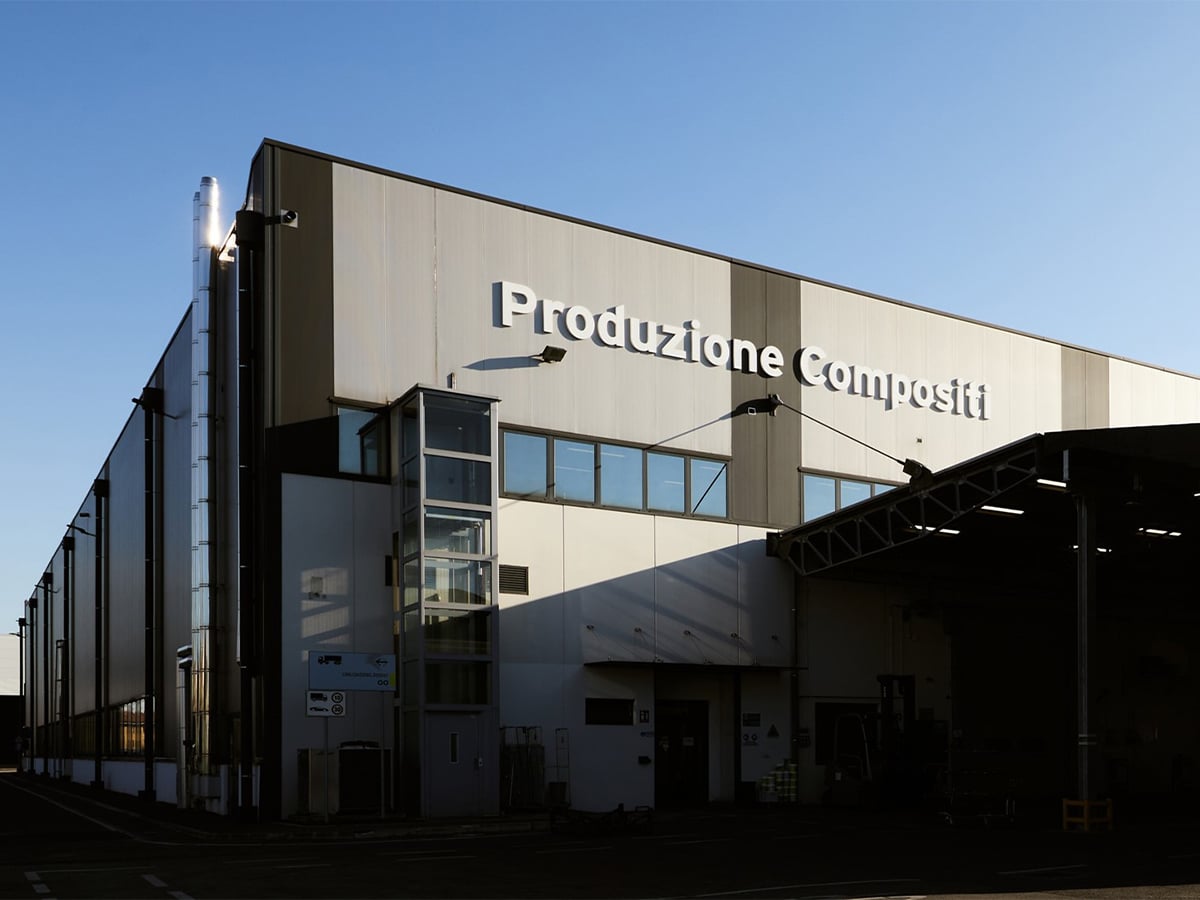
Everything Starts in Produzione Compositi
If you ask Lamborghini, their history of carbon fibre development started in 1983 when experts from Boeing arrived at the factory to set up the first composites department at Sant’Agata Bolognese. However, revisionist history tells us that a man called Horacio Pagani tried to start this process much earlier, but his request was denied by the head honchos at Lamborghini as it cost too much. He was never given the keys to an autoclave until it was time to create the Diablo.
Pagani would create the carbon fibre Lamborghini Countach Evoluzione in 1983 without an autoclave, finding a way to vacuum pack the materials to produce a lightweight end product. This would be used to create the Evoluzione, but also cars like the 25th Anniversary Countach, and eventually the Diablo, which marked the first production-level use of an autoclave and carbon fibre for Lamborghini.
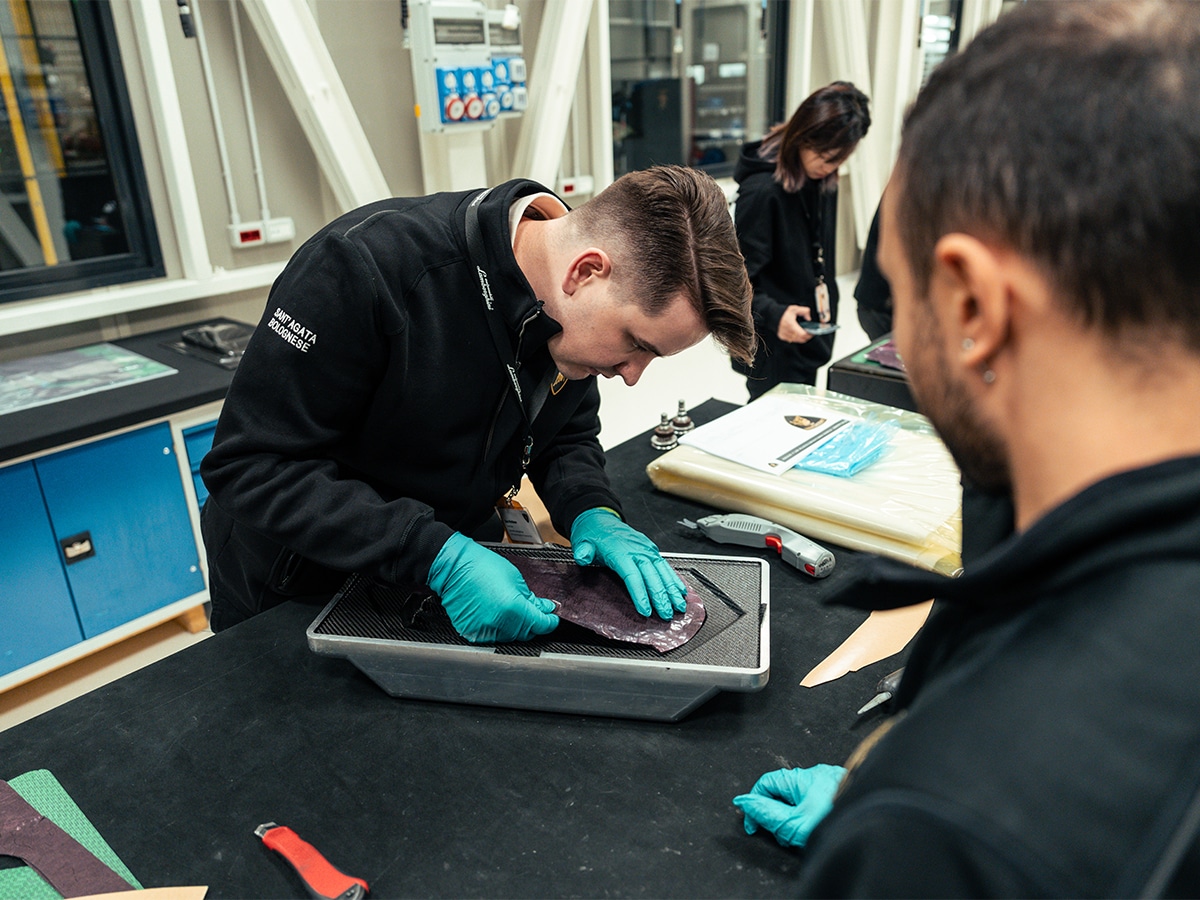
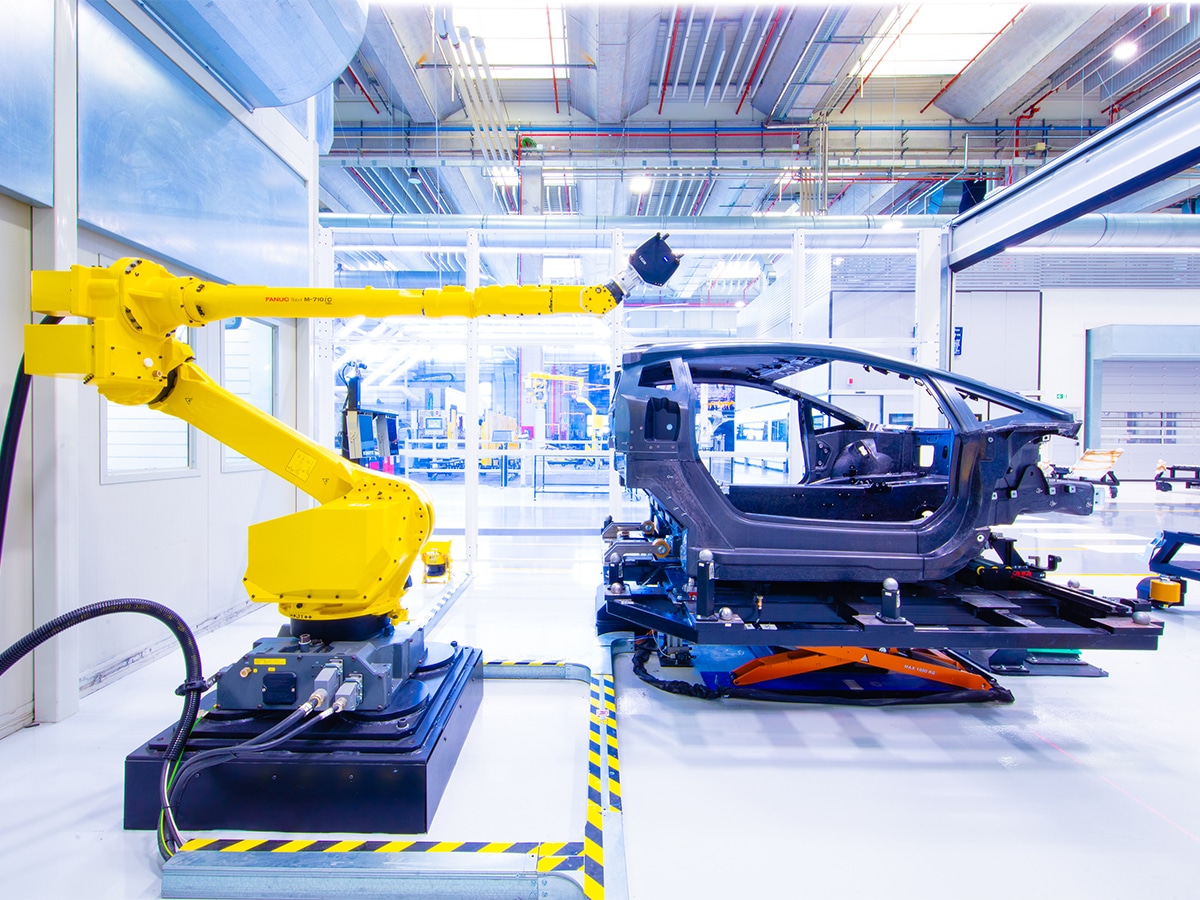
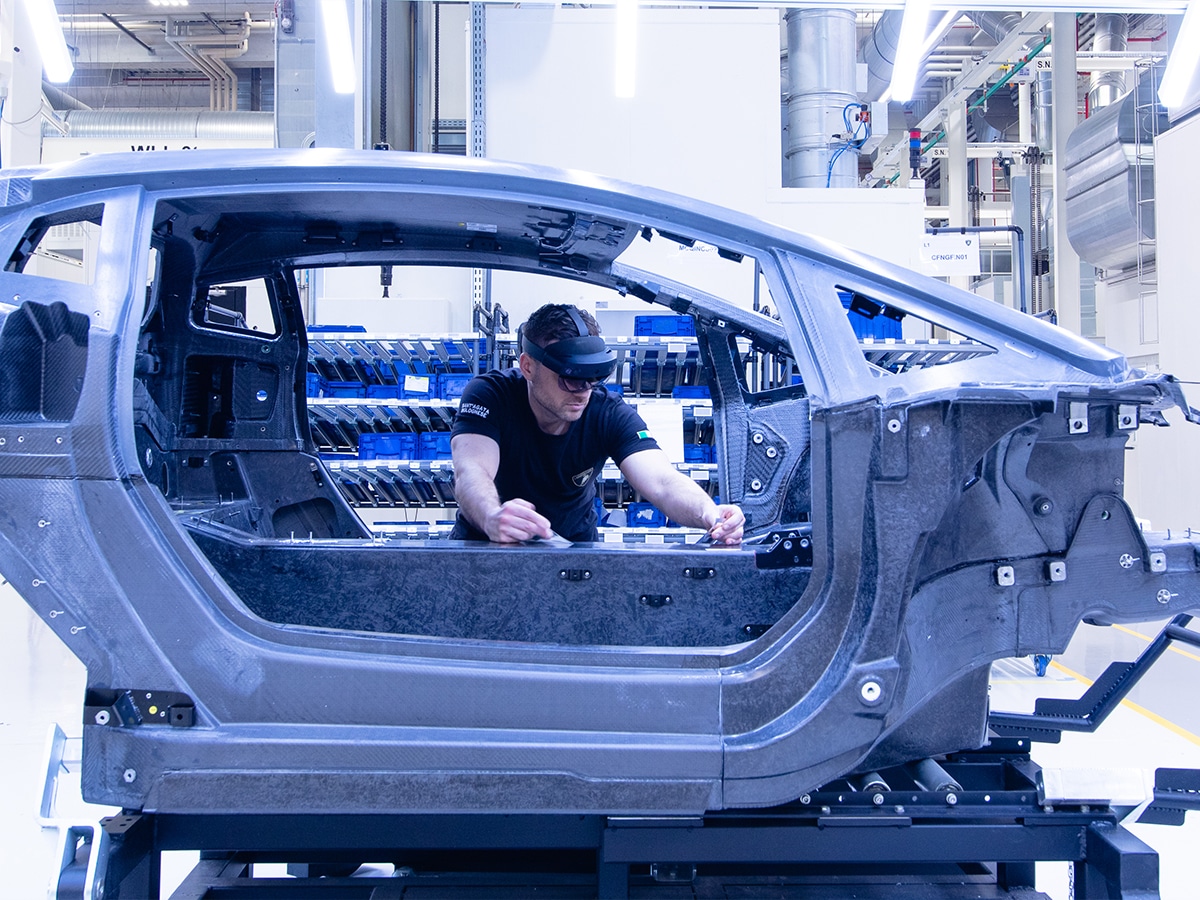
The most significant step in carbon fibre production for Lamborghini started in 2007 when they collaborated with the University Of Washington (UW) to develop RTM out-of-autoclave technology.
This process is complex, and you’d need a qualified engineer to explain it in detail, but it uses vacuum, pressure, and heat by means other than an autoclave and manual lamination to create carbon fibre that is without voids. This is a typical failure point, but it also allows the use of carbon fibre moulds, which is a game-changer for manufacturing. Lamborghini first used these moulds to create the Aventador monocoque, and now they’ve repurposed them for the Revuelto and Temerario.
Lamborghini can remain a leader in carbon fibre because few brands can match their manufacturing capability due to this patented RTM-Lambo technology. It’s impressive to witness how Lamborghini is staying ahead of the curve, and they probably need to be considering their shaky start with Pagani.
The brand uses this material throughout their vehicles, including but not limited to the main structural components, such as the monocoque of the Revuelto, but also the functional components like the ALA system (active aerodynamics system), and the aesthetic elements of the interior and exterior. Today, due to hybrid technology, this material is becoming even more important as lowering the weight of the vehicle is a necessity.
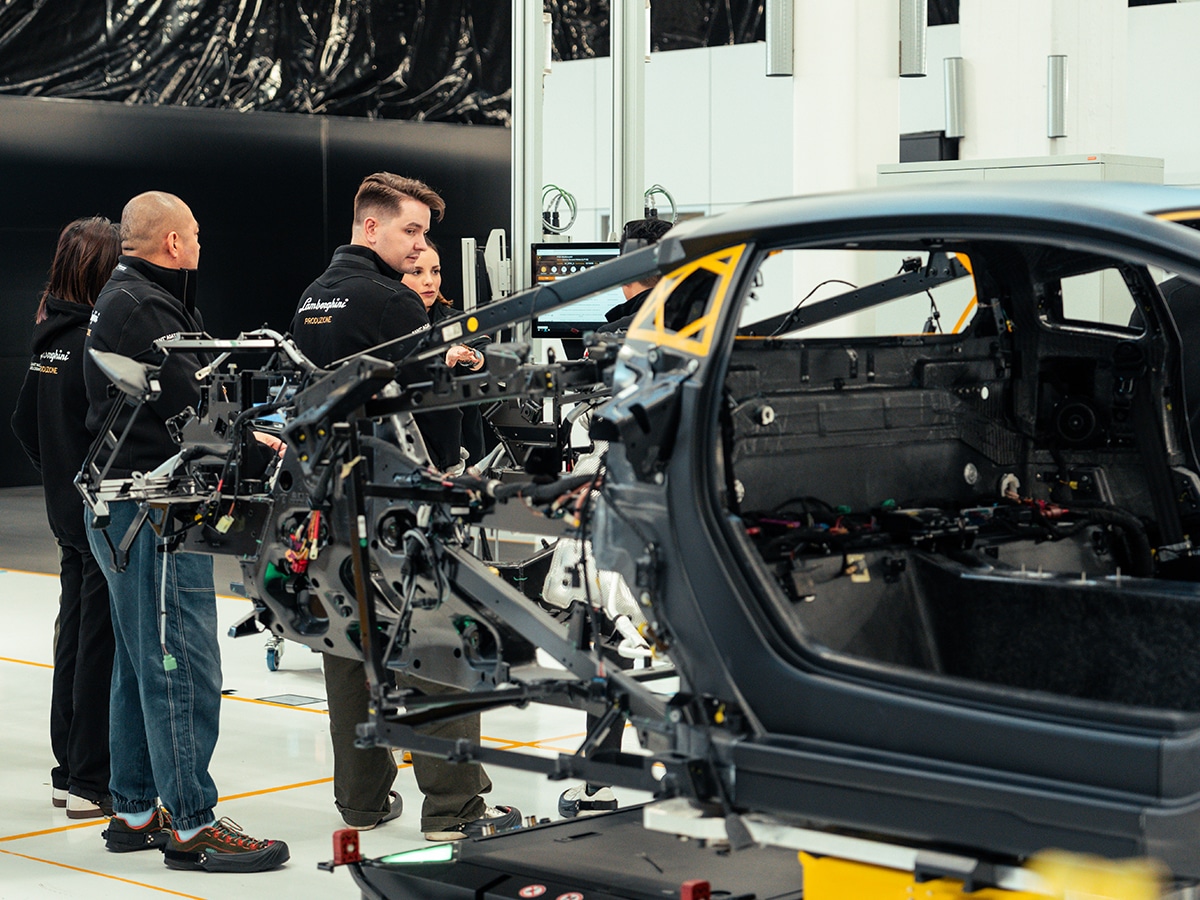
Once the Carbon Monocoque is Built, It’s Moved to the Line
Lamborghini gave us near unlimited access to their production line as part of this tour, and while our phones were locked up in a safe, we witnessed the entire process from raw carbon fibre to a completed vehicle.
This production capability at Sant’Agata Bolognese continues to expand and it now sits on a plot of land greater than 160,000 m2.
Production of the Urus SUV takes up a large amount of this space, but we began our two-day tour in the main building housing the assembly line for the new Revuelto and Temerario. This is best described as the place where the cars are screwed together (assembled), and it’s where the monocoque is delivered by AGVs (Automatic Guided Vehicles) after it’s finished being made at Produzione Compositi.
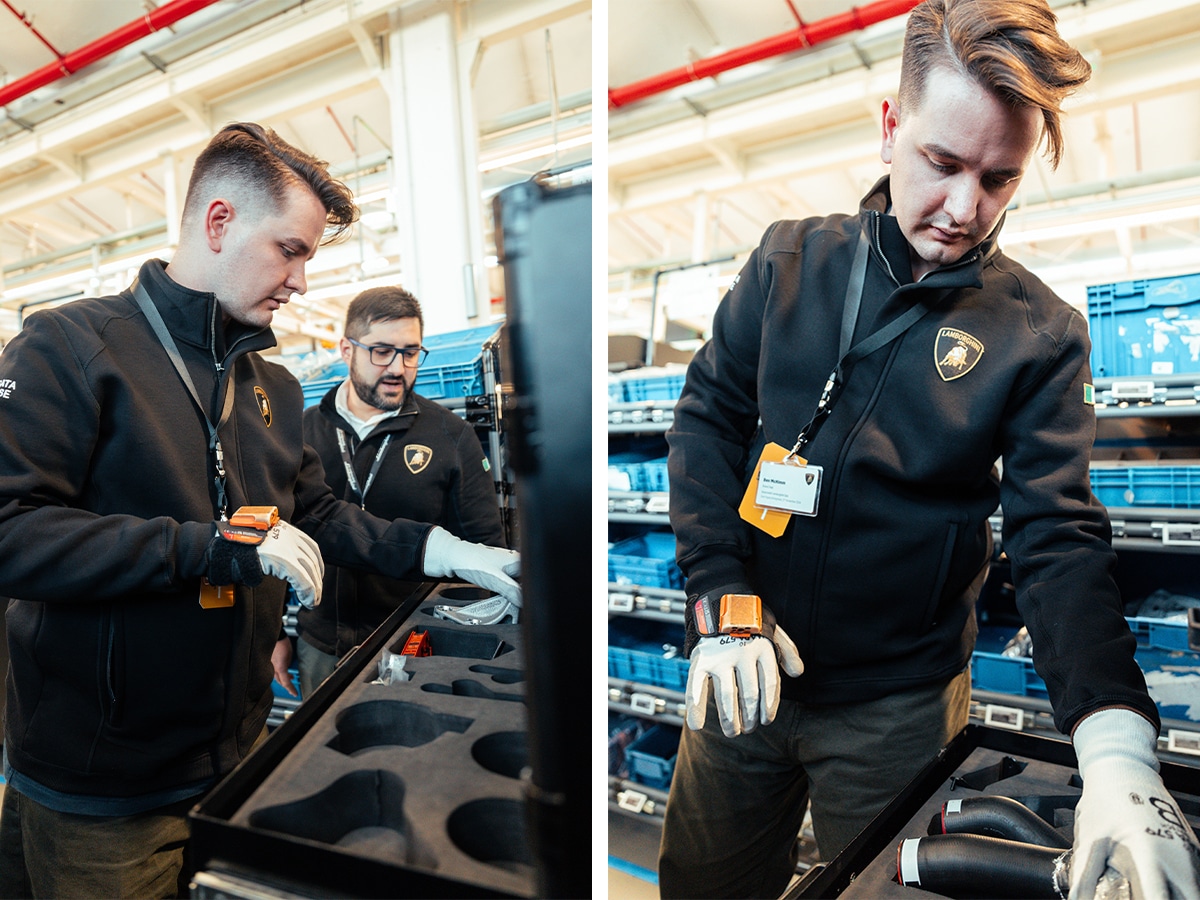
Picking the Parts
The first step of the process is to pick the correct parts, and that’s made easy by a scanning tool and flashing lights that tell you exactly where to reach, what part to pull out, and where to place it in the corresponding cut-out in the trolley. It’s processes like these that you wouldn’t immediately assume happen at factories, but it shows that even in lower-volume manufacturing, it’s important to track every step of the process for efficiency.
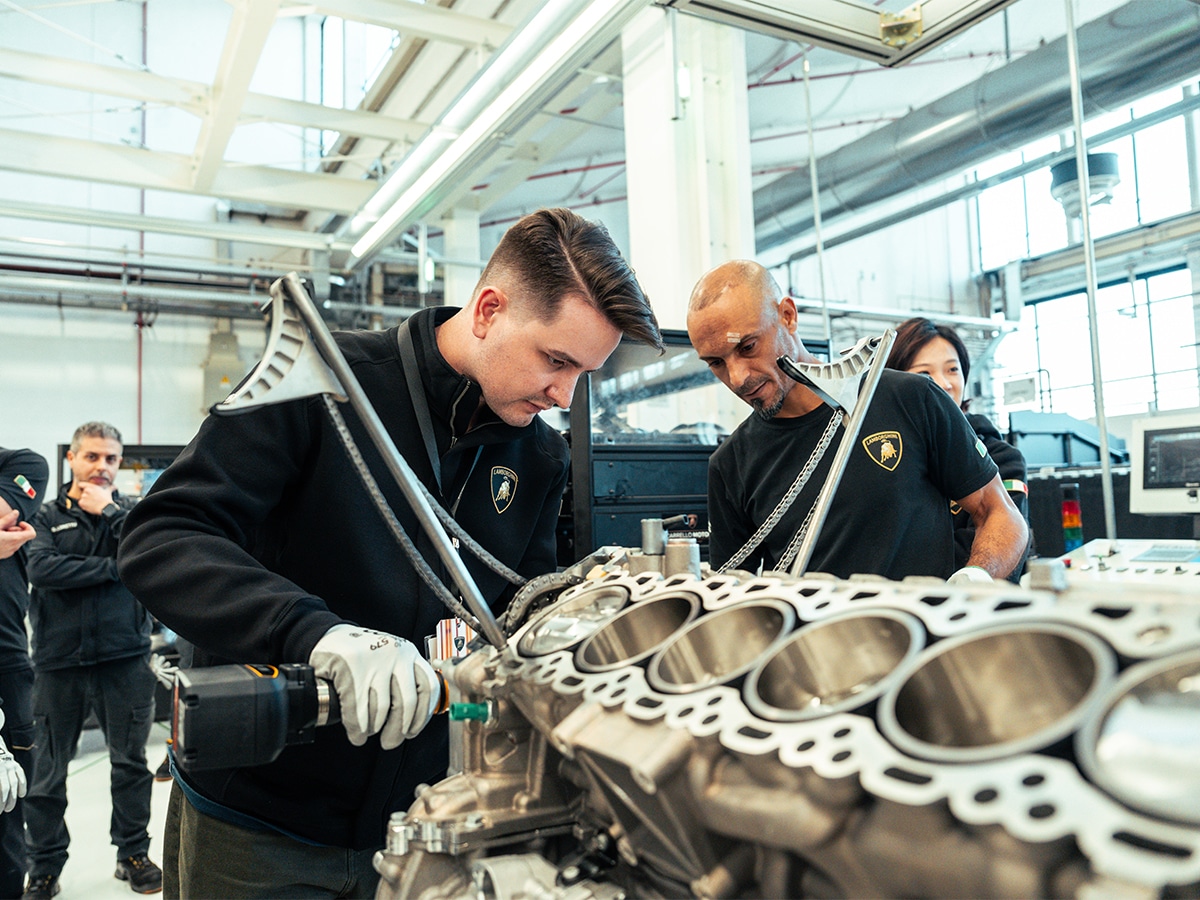
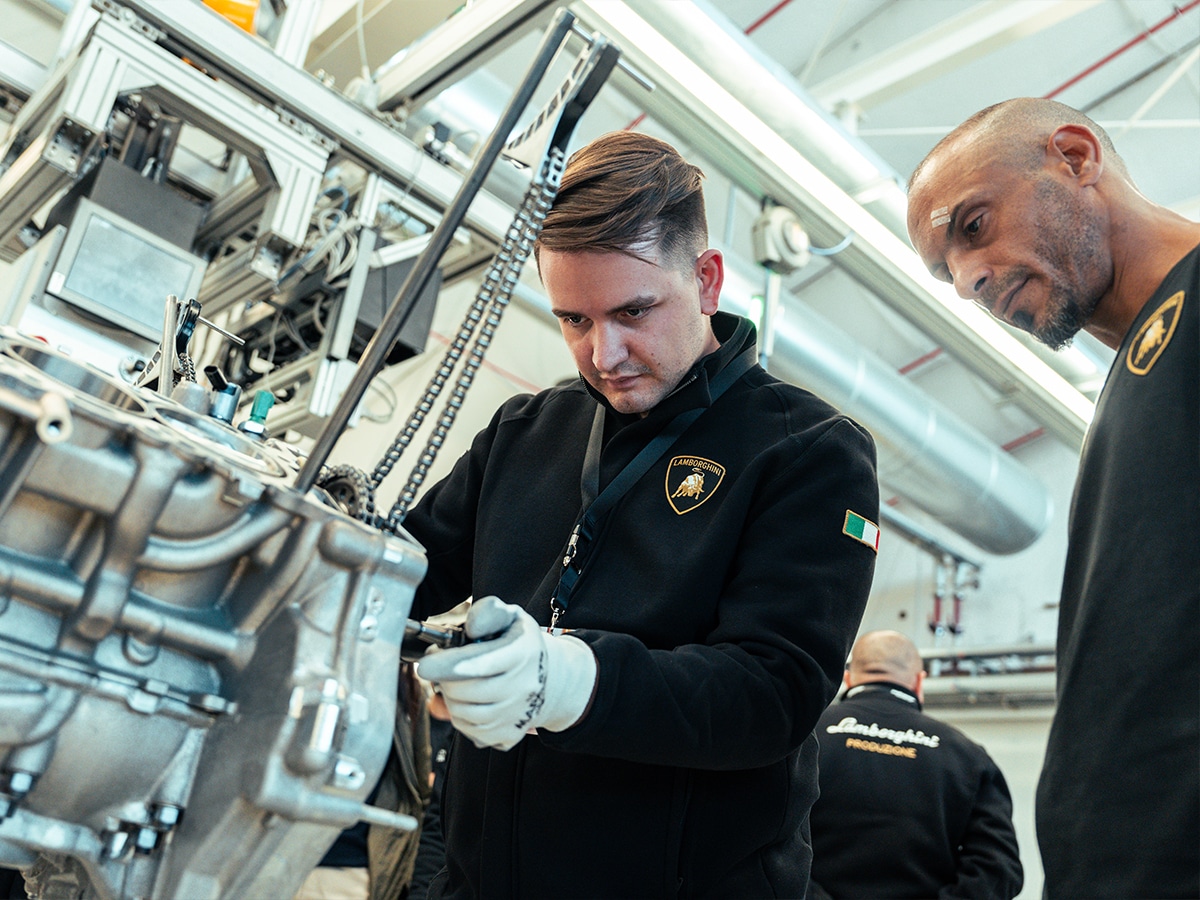
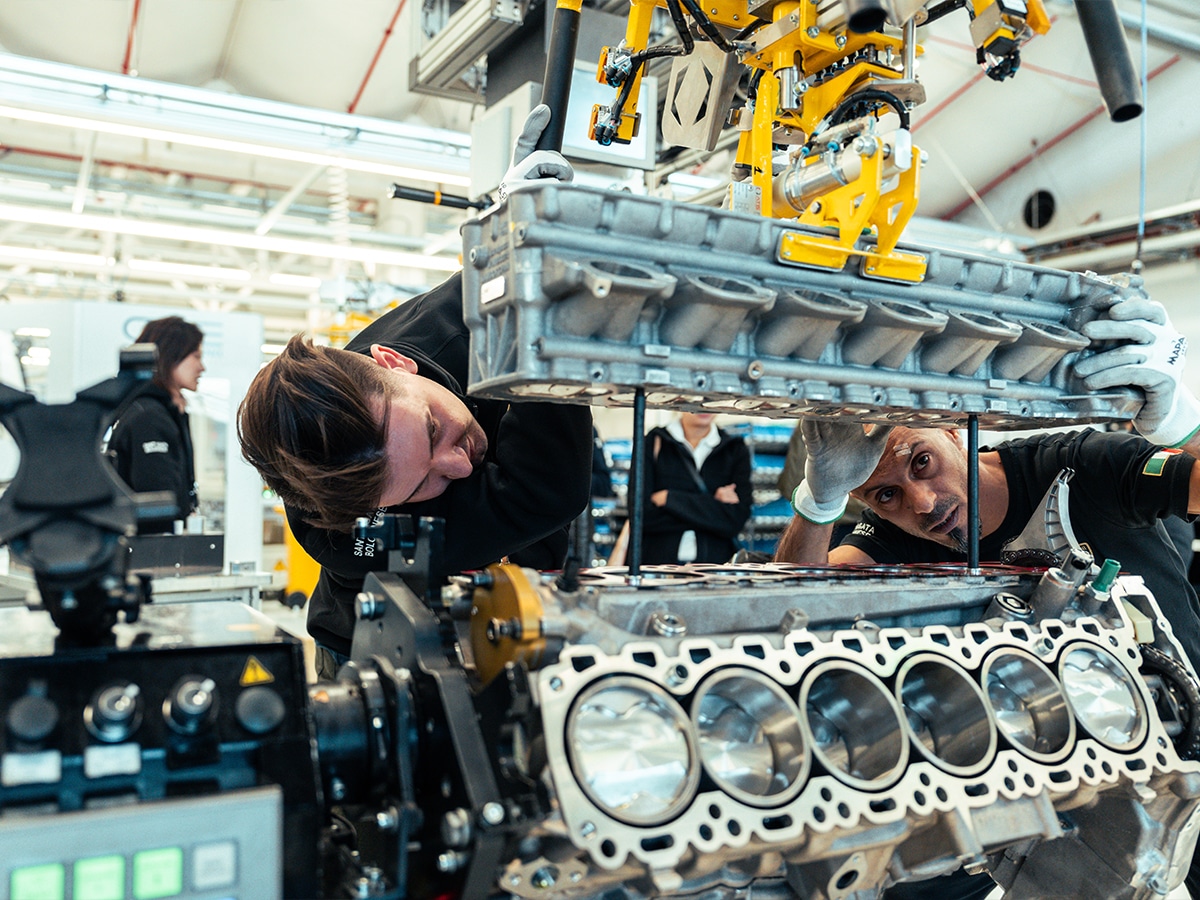
Torquing the Engine Components
Once the correct parts were selected, it was time to put the cylinder heads, timing chain, and cover on the Revuelto’s 6.5-litre V12 engine.
If you thought you knew how to use a torque wrench, think again. This particular tool is ultra-sensitive, which is good news for Revuelto buyers, but not great news for non-professionals who almost halted the whole assembly line because of too many errors. Still, it’s a satisfying thing to see an engine get put together (even though it was a dummy) and every step of the build process makes you question how Lamborghini makes any money from these cars because they’re that hands-on.
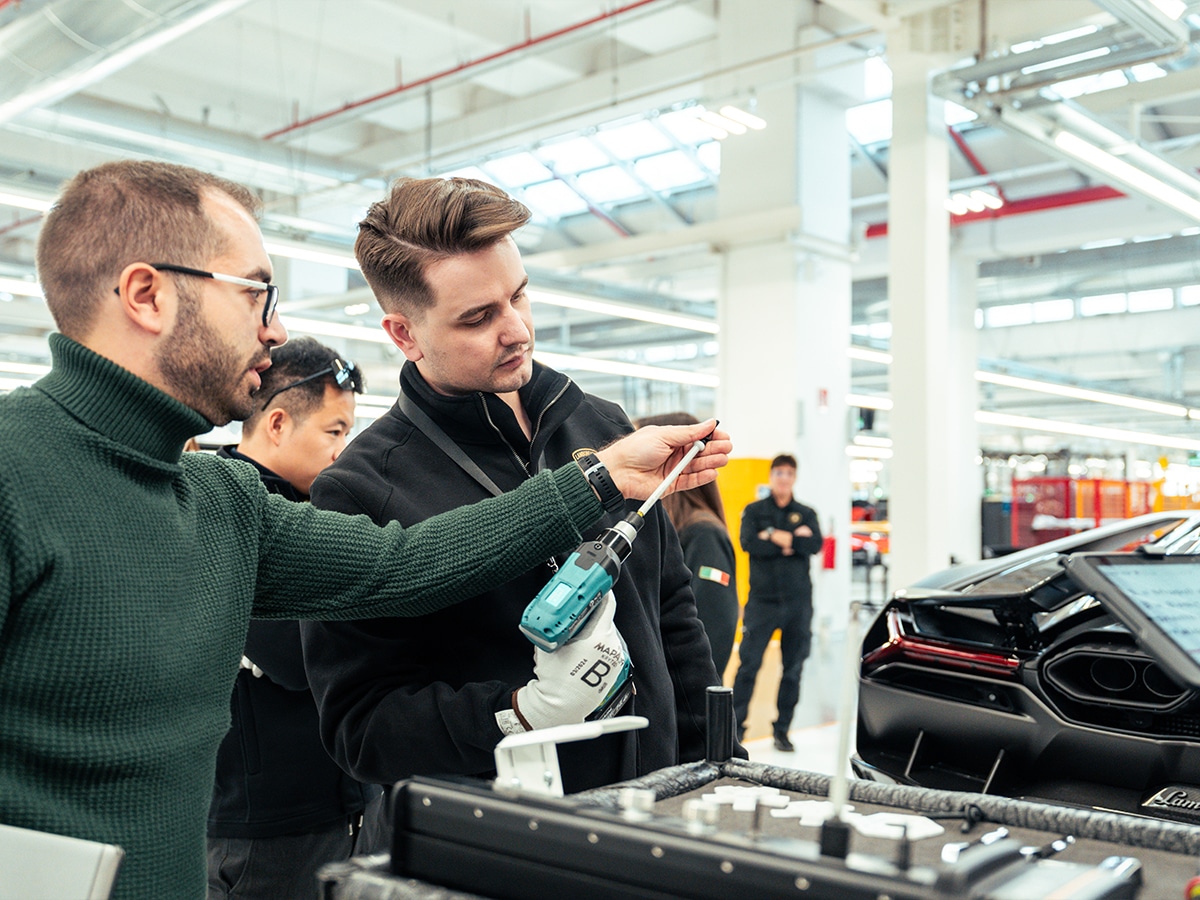
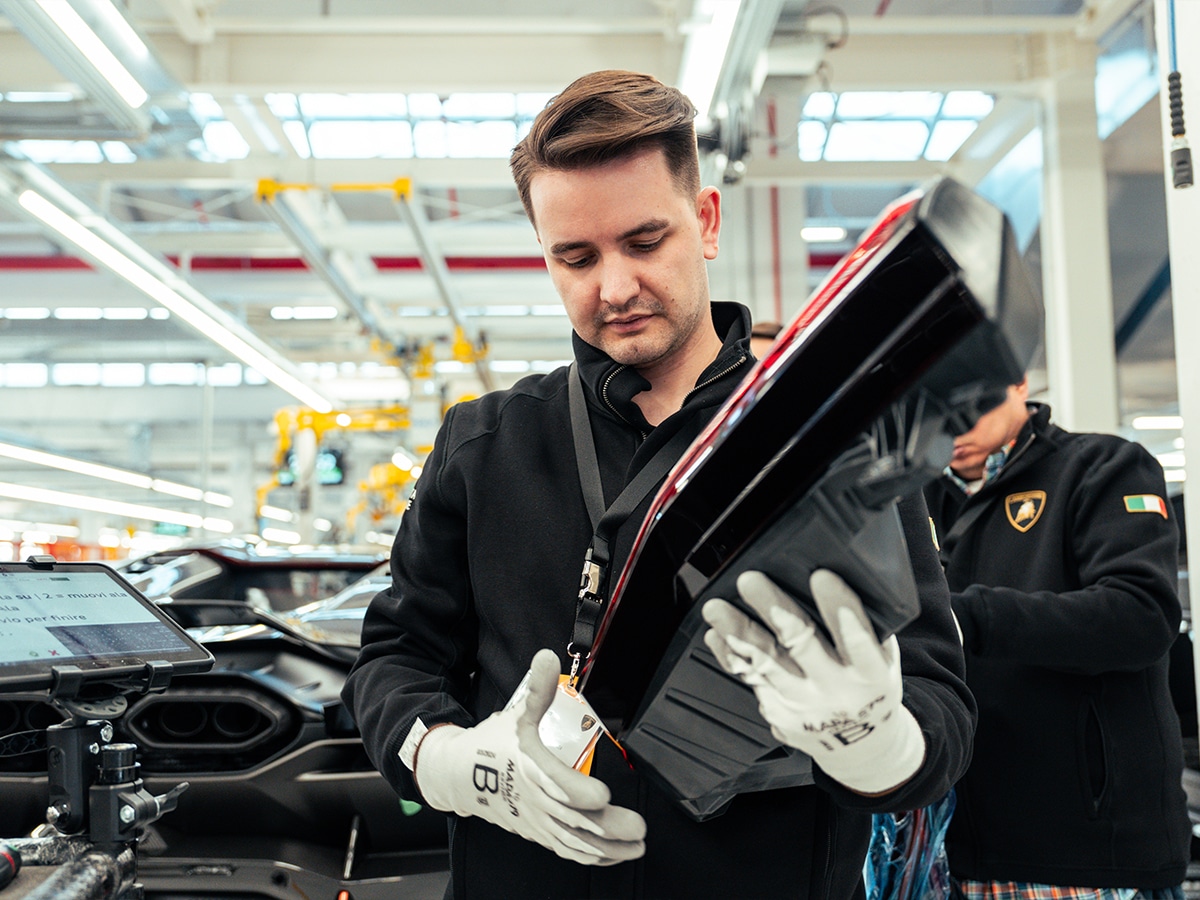
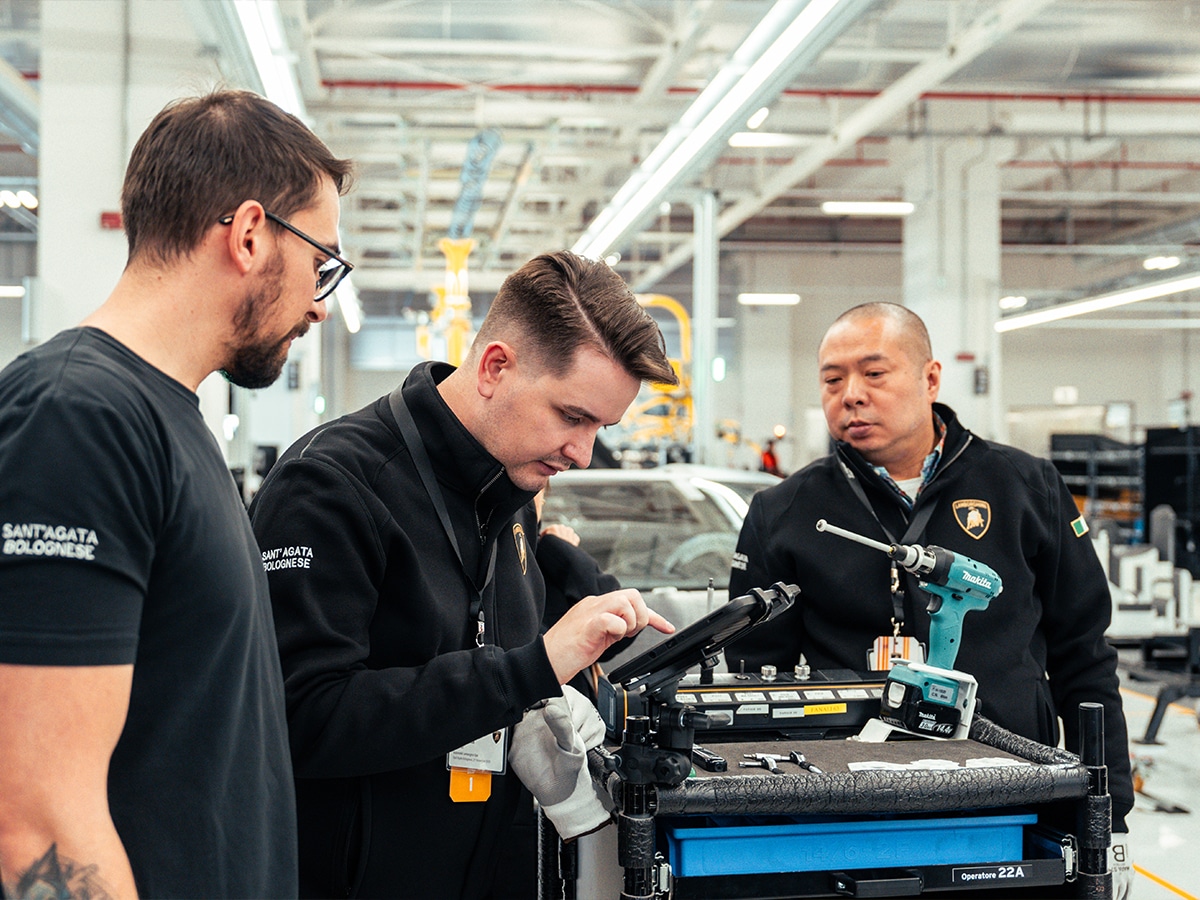
Attaching the Wing and Tail Lights
Once the parts were put on the engine we walked down the line and watched as the employees meticulously added the electric motor, battery, wiring harness, door cards, seats, dashboard, and interior pieces to the car before the fenders, bumpers, and exhaust were connected.
Then, it was time to get familiar with a tool that we knew how to use because the rear wing and tail lights had to be attached to a Revuelto.
With impact driver in hand, we cautiously added the screw to the magnetic tipped bit and successfully screwed the rear wing onto the car before putting it in the downforce position to access the bolt holes for the tail lights. This was easy enough, but losing the bolt in the engine bay of the car would’ve been a very embarrassing moment.
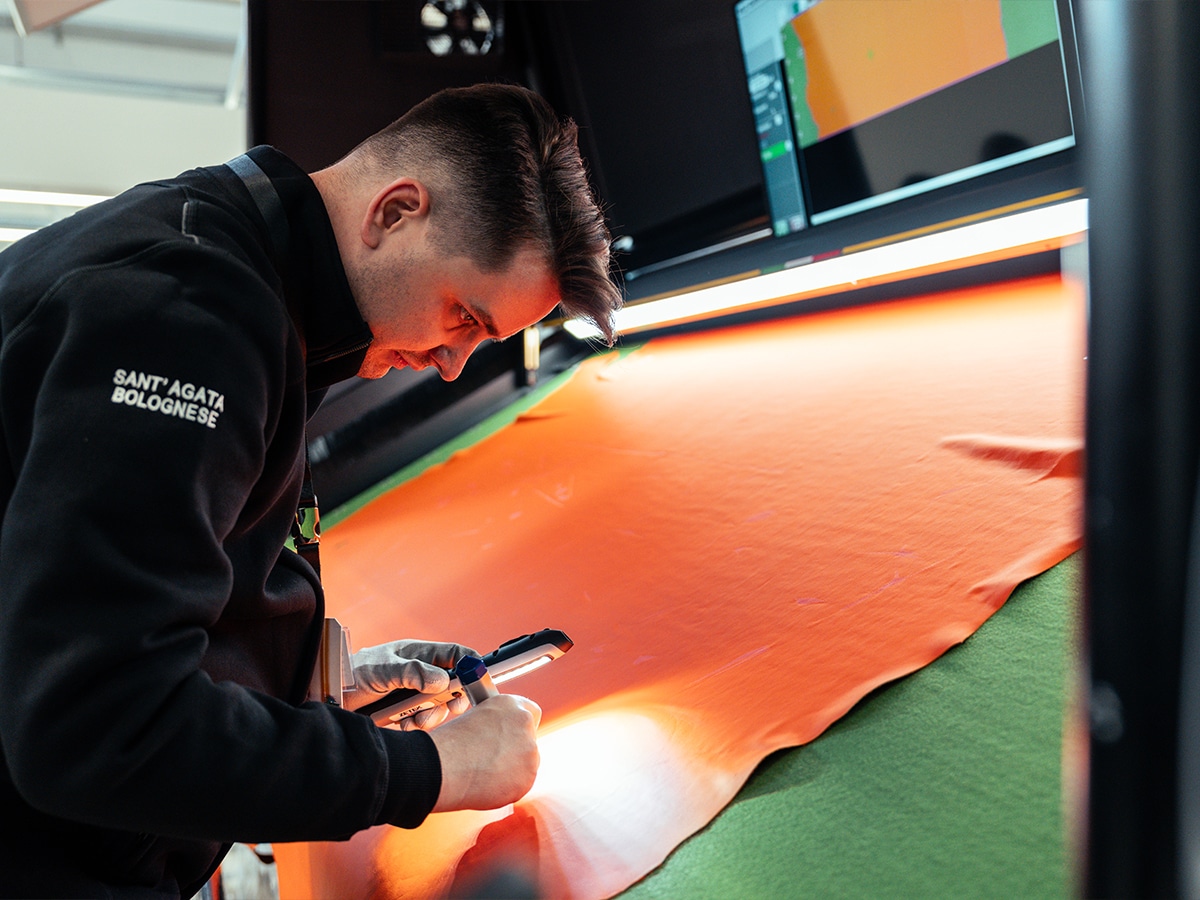
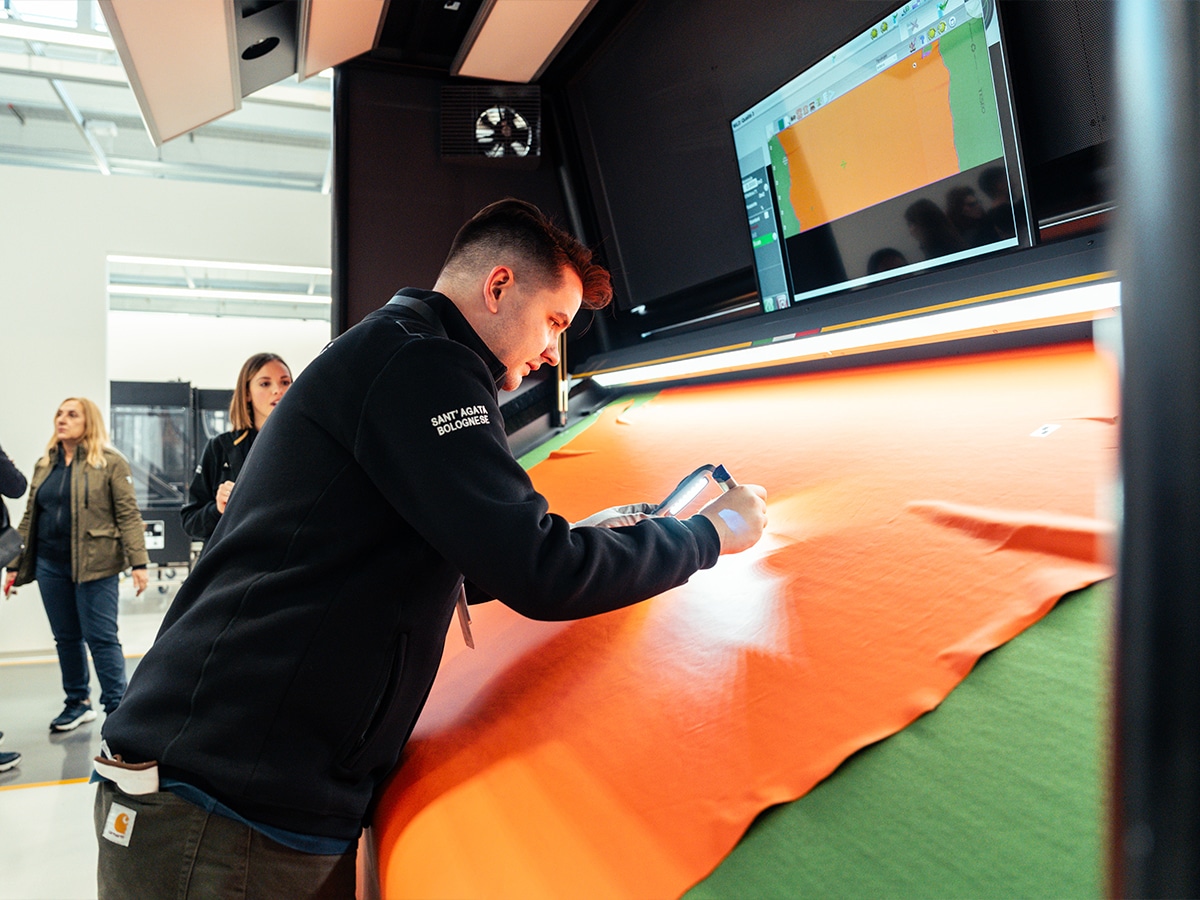
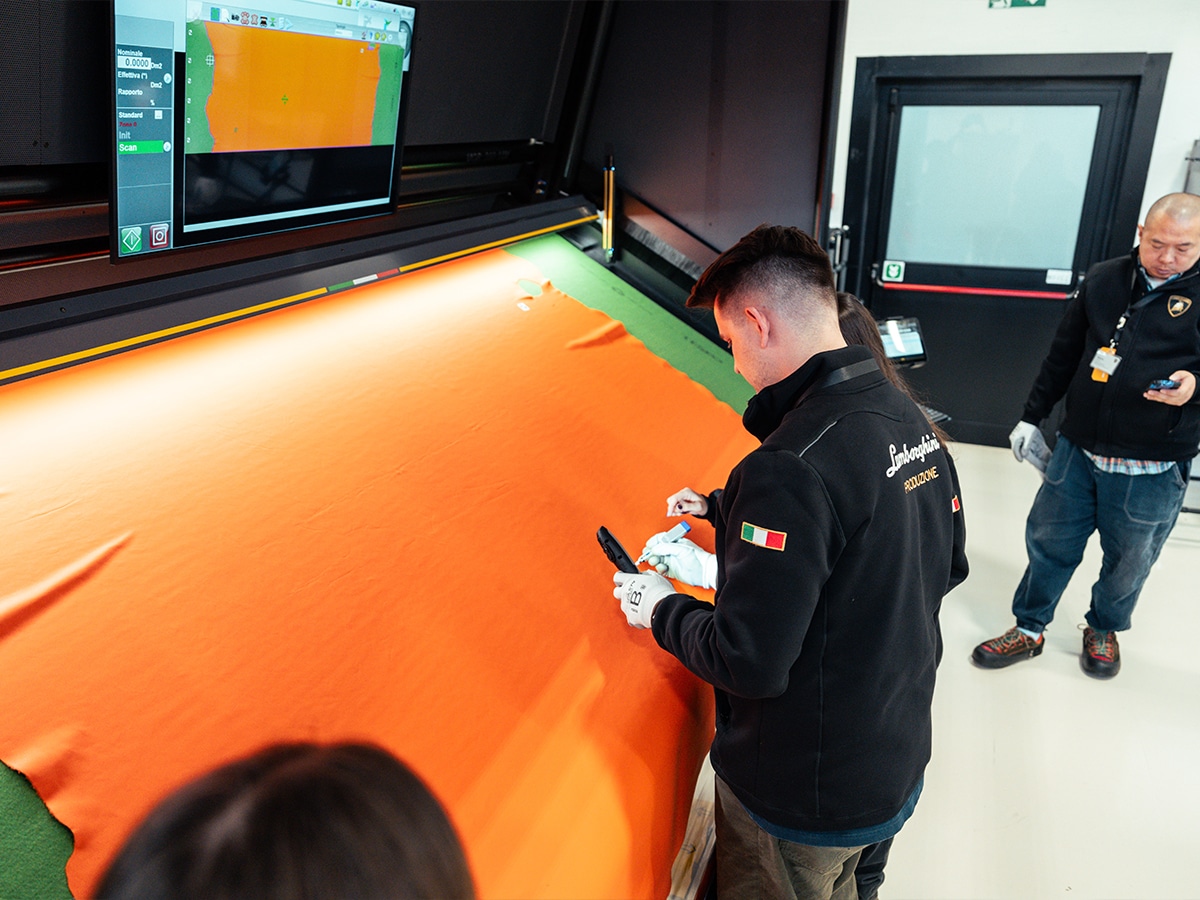
Leather and Upholstery
Finally, our tour ended at the saddlery where all of the leather and upholstery is added to the car. Here (above), you can see us inspecting the leather material for defects before it’s approved and sent through to the next stage of the process where it’s laser cut, stretched, and hand-moulded over the interior components. This is handbag-like leather and handled with the amount of care that you would expect.
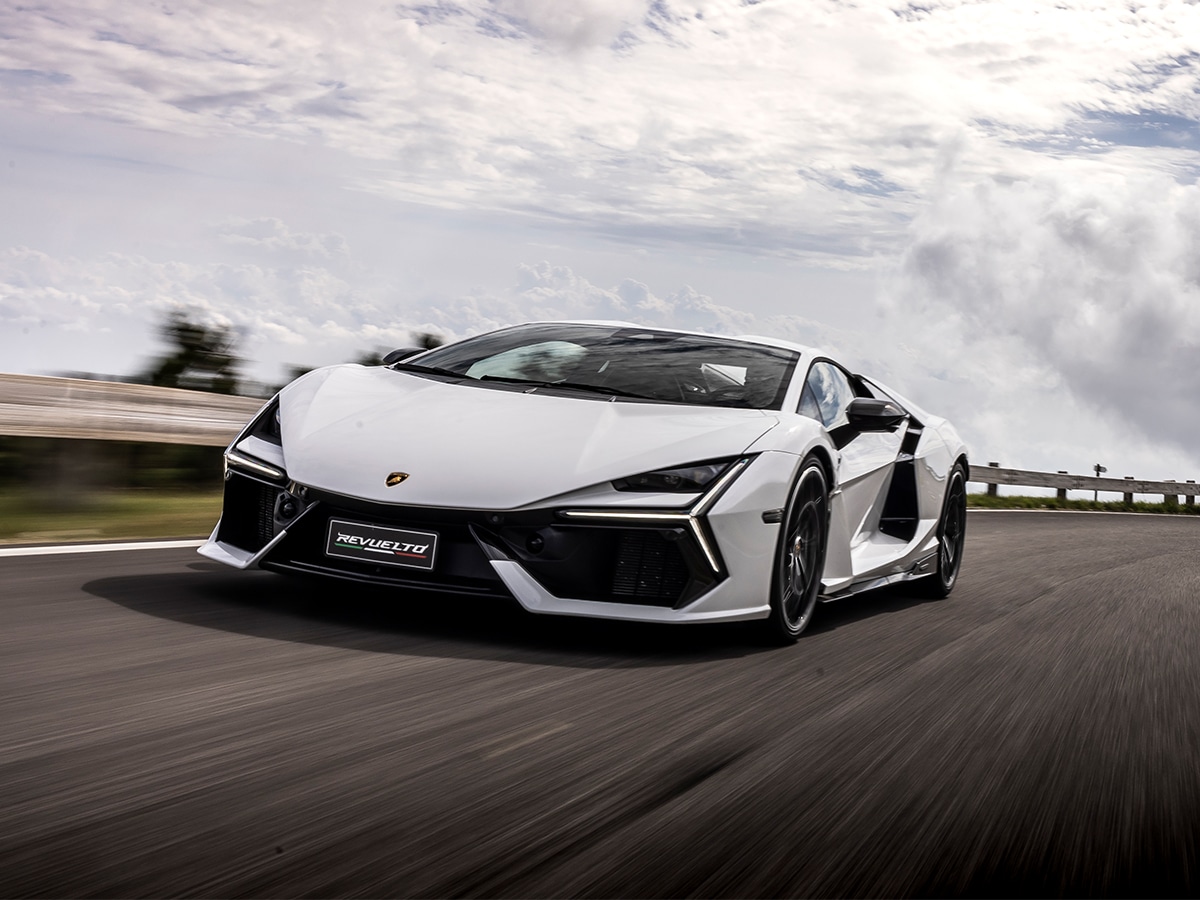
Time to Drive Some Lamborghini’s
This is seriously tiring work (trust us), and we were itching to get behind the wheel of some Lamborghini’s to blow off some steam after a hard morning on the tools. The brand was kind enough to hand us the keys to some new stuff and some old, including:
- Lamborghini Gallardo chassis no. 126
- 1 of 20 Lamborghini Murcielago ‘Versace Edition’
- Revuelto
- Urus SE
Without having completed the full factory tour, we would never have realised the amount of time, effort, and expertise that has gone into these vehicles. You can drive the cars and realise this for the most part, but you never truly understand a brand until you visit their factory and meet the people assembling these dream cars. It’s important to remind yourself where these cars come from, the technology that goes into them, and above all else, the passion. Everyone who works in the Lamborghini factory lives, breathes, and sweats the brand. It’s not simply passion, it’s in their blood.
We have full reviews of each of these cars coming soon, so stay tuned, but for now, check out the Lamborghini Museum below, and plan a trip to Sant’Agata Bolognese.
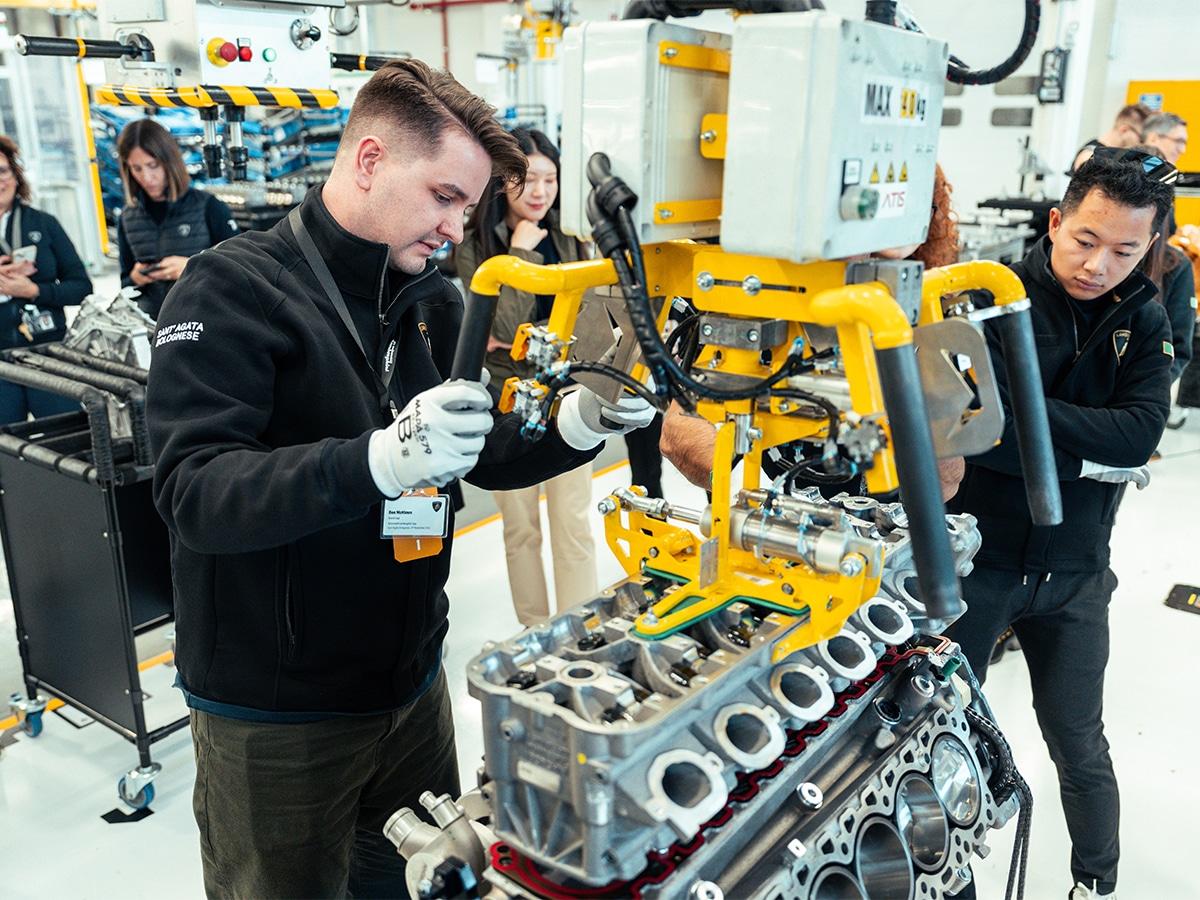
You’ll also like:
Comments
We love hearing from you. or to leave a comment.